PCB打样厂家(凡亿PCB)作为专业的PCB线路板制造商,专注于高精密多层板、阻抗板的研发,以及PCB打样和中小批量板的生产制造。今天就让凡亿PCB带大家一起了解一下PCB短路及改善方法。
内容摘要: 退膜药水浓度高,退膜时间长,抗镀膜早已掉落,可板仍在强碱溶液中浸泡,部分锡粉附在铜箔表面上,蚀刻时有一层很薄的金属锡护着铜表面,起到抗蚀作用,造成要去除的铜未除干净,从而导致线 路短路。所以我们需要严格控制好退膜药水的浓度、温度、退膜时间,同时退膜时用插板架插好,板与板 之间不能层叠碰在一起。
一、PCB在跑锡造成的短路:
1、在退膜药水缸里操作不当引起跑锡;2、已退膜的板叠加在一起引起跑锡。
改善方法:(1)退膜药水浓度高,退膜时间长,抗镀膜早已掉落,可板仍在强碱溶液中浸泡,部分锡粉附在铜箔表面上,蚀刻时有一层很薄的金属锡护着铜表面,起到抗蚀作用,造成要去除的铜未除干净,从而导致线 路短路。所以我们需要严格控制好退膜药水的浓度、温度、退膜时间,同时退膜时用插板架插好,板与板 之间不能层叠碰在一起。
(2)已退膜的板未烘干便叠加在一起,使得板与板之间的锡浸在未烘干的退膜溶液中,部分锡层会溶 解附在铜箔表面上,蚀刻时有一层很薄的金属锡护着铜表面,起到抗蚀作用,造成要去除的铜未除干净, 从而导致线路短路。
二、PCB蚀刻不净造成的短路:
1、蚀刻药水参数控制的好坏直接影响到蚀刻质量,目前我司使用的是碱性蚀刻液,具体分析如下:1.1 PH值:控制在8.3~8.8之间,如果PH值低了,溶液将变成粘稠状态,颜色偏白色,蚀板速率下降 ,这种情况容易引起侧腐蚀,主要通过添加氨水来控制PH值。 1.2 氯离子:控制在190~210g/L之间,主要通过蚀刻盐对氯离子含量进行控制,蚀刻盐是由氯化铵和 补充剂组成的。1.3 比重:主要通过控制铜离子的含量来对比重进行控制,一般将铜离子含量控制在145~155g/L之间 ,每生产一小时左右进行检测一次,以确保比重的稳定性。1.4 温度:控制在48~52℃,如果温度高了氨气挥发快,将造成pH值不稳定,且蚀刻机的缸体大部分 都是由PVC材料制作的,PVC耐温极限为55℃,超过这个温度容易造成缸体变形,甚至造成蚀刻机报废,所 以必须安装自动温控器对温度进行有效监控,确保其在控制范围之内。1.5 速度:一般根据板材底铜的厚度调整合适的速度。建议:为了达到以上各项参数的稳定、平衡,建议配置自动加料机,以控制好子液的各项化学成份,使蚀刻液的成份处于比较稳定的状态。2、整板电镀铜时电镀层厚薄不均匀,导致蚀刻不干净。改善方法:(1)全板电镀时尽量实现自动线生产,同时根据孔面积的大小,调整好单位面积的电流密度(1.5~2.0A/dm2),电镀时间尽量保持一致,飞巴保证满负荷生产,同时增加阴、阳极挡板,制定“电镀边条”的使用制度,以减少电位差。(2)全板电镀如果是手动线生产,则板大的需要采用双夹棍电镀,尽量使单位面积的电流密度保持一 致,同时安装定时报警器,确保电镀时间的一致性,减少电位差。
三、PCB可视微短路:
1、曝光机上迈拉膜划伤造成的线路微短路;2、曝光盘上的玻璃划伤造成的线路微短路。改善方法:(1)曝光机上的迈拉膜因使用时间较长,膜面上有划伤现象,划痕积聚有灰尘形成黑色或不透明的“小线条”,在线路图形曝光时因黑色或不透明的“小线条”遮光,使得显影后在线路之间形成露铜点而造 成短路,且板件上的铜箔越薄越容易短路,线间距越小越容易短路。所以当我们一经发现迈拉膜有划伤现 象时,必须马上进行更换或用无水酒精清洁,保证迈拉膜的透明度,严格控制不透明的划痕存在。(2)曝光机上曝光盘玻璃因使用时间长,玻璃表面上有划伤现象,划痕积聚有灰尘形成黑色印子或不 透明的“小线条”,同样在线路图形曝光时因不透明的“小线条”遮光,显影后在线之间形成露铜点而造 成短路。所以当我们一经发现有玻璃划伤现象时,必须马上进行更换或用无水洒精进行清洁,严格控制不 透明的划痕存在
四、夹膜短路:
1、抗镀膜层太薄,电镀时因镀层超出膜厚,形成夹膜,特别是线间距越小越容易造成夹膜短路。2、板件图形分布不均匀,孤立的几根线路在图形电镀过程中,因电位高,镀层超出膜厚,形成夹膜 造成短路。改善方法:(1)增加抗镀层的厚度:选择合适厚度的干膜,如果是湿膜可以用低网目数的网版印制,或者通过印 制两次湿膜来增加膜厚度。(2)板件图形分布不均匀,可以适当降低电流密度(1.0~1.5A)电镀。在日常生产中,我们出于要保证 产量的原因,所以我们对电镀时间的控制通常是越短越好,所以使用的电流密度一般为1.7~2.4A之间,这 样在孤立区上得到的电流密度将会是正常区域的1.5~3.0倍,往往造成孤立区域上间距小的地方镀层高度 超过膜厚度很多,退膜后出现退膜不净,严重者便出现线路边缘夹住抗镀膜的现象,从而造成夹膜短路, 同时会使得线路上的阻焊厚度偏薄。
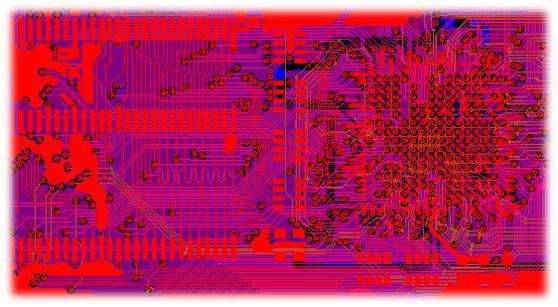
五、看不见的微短路:
看不见的微短路对我司来说,是困扰最久也曾经是最难解决的问题,在测试出现问题的成品板中,50%左右是属于此类微短路的问题,其主要原因是线间距内存在着肉眼无法看见的金属丝或金属颗粒。改善方法:1、因阻焊前磨板是采用物理粗化方式的,磨刷痕深度一般在0.3~1.5μm之间,磨板过程中由于板边 沿有大量的金属碎屑附着板面,压力水洗时有部分未冲洗干净,附在水洗后面的海棉吸水辊表面,当后面 再继续过板时,则金属碎屑就有可能附在板面上,从而造成成品板有许多肉眼看不见的短路现象,那么为 了避免这类现象,我们必须定期对海棉吸水辊进行清洗,这一点非常重要,而且也非常容易被人疏忽!2、磨板后面水洗水定期更换,确保水洗缸的水保持清洁。3、磨板机定期清洁、保养(用3~5% NaOH溶液和3~5% H2SO4溶液分别清洗),清洁水槽铜粉积聚物和水 中的微生物体,风干段内部及风机过滤器定期清洁并保持干净。
六、固定位短路 :
主要原因是菲林线路有划伤或涂覆网版上有垃圾堵塞,涂覆的抗镀层固定位露铜导致短路。改善方法:1、菲林底片不得有沙眼、划伤等问题,放置时药膜面要朝上,不得和其它物体摩擦,拷片时药膜面 对药膜面进行操作,用完后及时装入合适的菲林薄膜袋中保存。2、对位时药膜面对板面,取菲林时用双手对角拿起,不要碰到其它物体,避免药膜面划伤,每张菲 林对板到一定数量时须停止对位进行专人检查或更换,用完后装入合适的菲林薄膜袋中保存。3、操作人员手上不得佩戴任何装饰物如戒指、手镯等,指甲要常修剪并保持园滑,对位台表面不得 放任何杂物,台面保持干净平滑。4、网版生产前一定要严格检查,确保网版无不通现象,涂覆湿膜时经常要抽检,检查是否有垃圾堵 塞网版。当间隔一段时间没有印刷时,印刷前要空网先印刷几次,使油墨内的稀释剂充分溶解凝固的油墨 ,确保网版漏油畅通。
七、划伤短路:
1、涂覆湿膜后划伤,对位时操作不当造成膜面划伤。2、显影机出口接板忙不过来造成板与板之间碰撞划伤。3、电镀时取板不当,上夹板时操作不当,手动线前处理过板时操作不当等造成划伤。改善方法:(1)因涂覆湿膜后在插板时容易造成划伤,所以板与板之间最好间隔远一点,确保板面无划伤现象。对位时双手取、放板,严格避免板与板叠加在一起,或板与对位台面摩擦,避免划伤板面。(2)显影时根据板的大小及接板人的操作能力调整放板的间隔距离,出板口无人接板时机器入板处不 得放板,接板时用双手卡板,避免板与板之间产生碰撞造成板面划伤。(3)电镀时双手取、放板,避免两块板或多块板层叠在一起进行夹板,手动线上板时避免板与台面之 间的摩擦,手动线前处理的板不能过多,过板时一夹一夹地过板避免碰撞。
凡亿PCB专业的PCB厂家,PCB设计解决服务商,专注于PCB行业的发展,值得信赖。